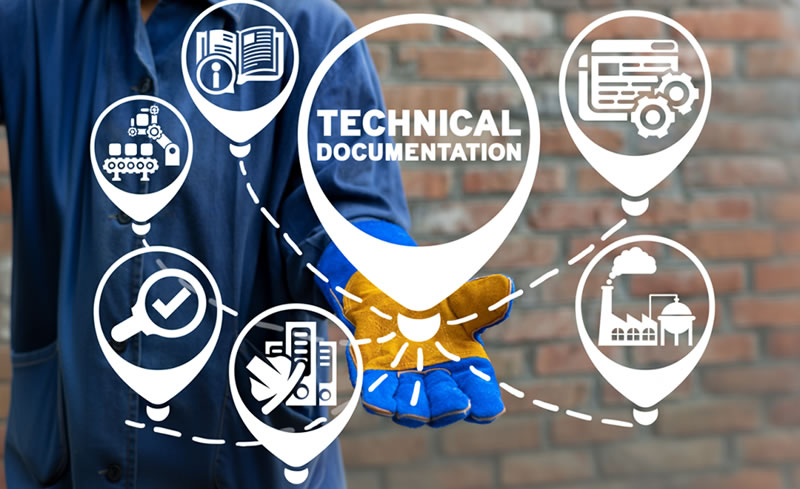
Part 1: reaction mechanisms and the role of porosity – David Lankard, Lankard Materials Laboratory Inc, Ohio, US, and Katherine Fleeman and Kassandralee Barrett, Allied Minerals Products.
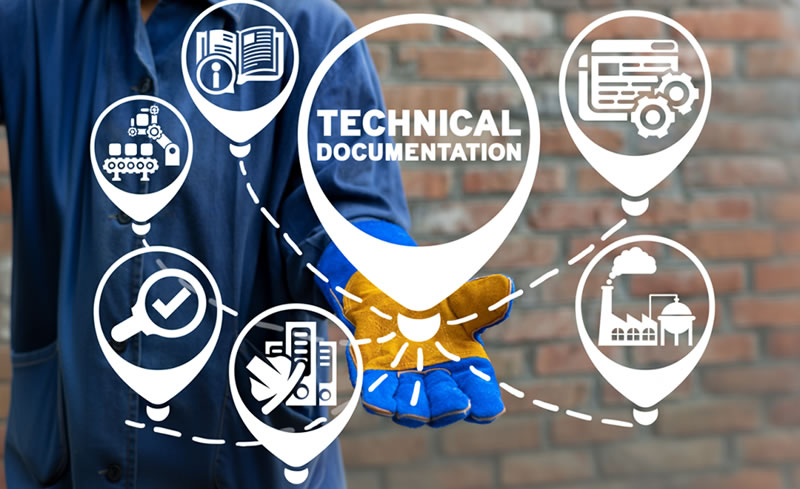
Abstract
Although the attack of aluminosilicate refractories by alkalis has been the subject of study for at least fifty years, it continues to be a problem today. In the present study, a fine grained mullite-based castable was used to gain a better understanding of what is going on at the microstructural level when sodium slag comes into contact with mullite. The castable had been developed in a previous study of alkali-testing methodology at Allied Mineral Products. Polished thin sections were used to characterise the microstructure of the castable following exposure to sodium carbonate slag at 1370 degrees C.
Pre-test and post-test chemical data was obtained using XRF analyses, with XRD analyses used to identify crystalline mineral phases. The important role of refractory porosity in controlling the extent of alkali attack damage is illustrated and discussed.
Introduction
The Na2O-SiO2-Al2O3 phase diagram (fig.1) shows the fate of mullite as the Na2O content of the environment increases. A join line connects mullite with Na2O in this view. At low sodium levels mullite can persist in equilibrium with nepheline and alumina (or beta alumina). At increased levels of sodium, mullite is gone as a stable phase, as the composition enters the alumina-nepheline-sodium aluminate phase field.
The soda-mullite join line crosses the nepheline-sodium aluminate join around midway. The binary nepheline-sodium aluminate phase diagram, shown in fig.2 in the article in the IRE journal June 2025, reveals that these minerals form a complete solid solution system. Carnegieite is the high temperature form of nepheline. Nepheline/carnegieite melts at 1526°C and sodium aluminate melts at 1885°C. There are six distinct solid solution phases for which XRD data have been obtained(3). The distinction for the solid solution phases is made on the basis of the silica content, which ranges from zero in sodium aluminate to one hundred per cent in nepheline.
Five of the six Na-Al-O solid solution phases crystallise in the orthorhomic or tetratgonal system, resulting in long, thin acicular particles. In the present study, a fine grained castable was formulated to produce a near one hundred per cent mullite refractory when fired. This was accomplished.
Two mullite compositions were developed for which the primary intended variable is the porosity level. For mullite Composition 7, the ASTM C20(4) porosity was 25 per cent. For mullite Composition 8, the C20 porosity was near zero. Composition 8 survived the sodium exposure cup test at 1370°C, while Composition 7 disintegrated.
The full paper is published in The Refractories Engineer 2025: Issue 2 – June.
#IRE #Institute #Refractories #Engineers #Journal #Conference #Training