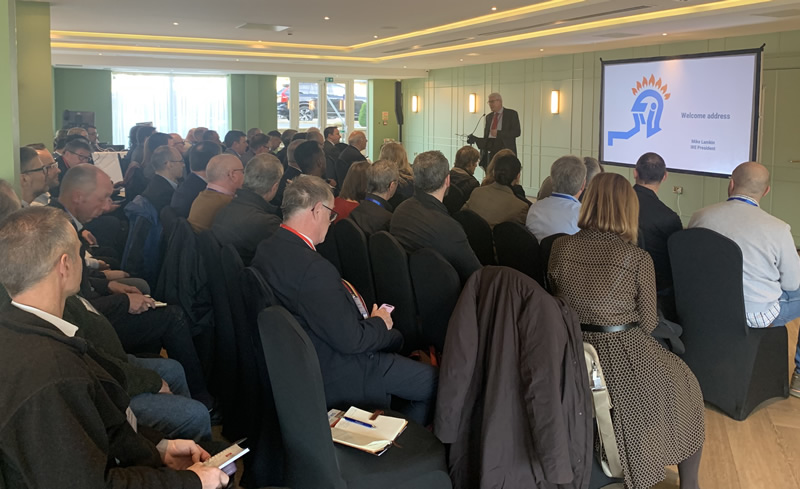
Held on 13 November at Wildes Inns in Derbyshire (UK), the annual IRE Conference attracted a good attendance in what is considered a difficult time for manufacturing, which is of course impacting the refractories industry.Nevertheless, delegates turned out to listen to some high quality speakers impart their knowledge on a range of subjects, including refractories and hydrogen; zero carbon dioxide refractories; sustainability of recycled refractories; and alumina containing insulating materials; plus many others.
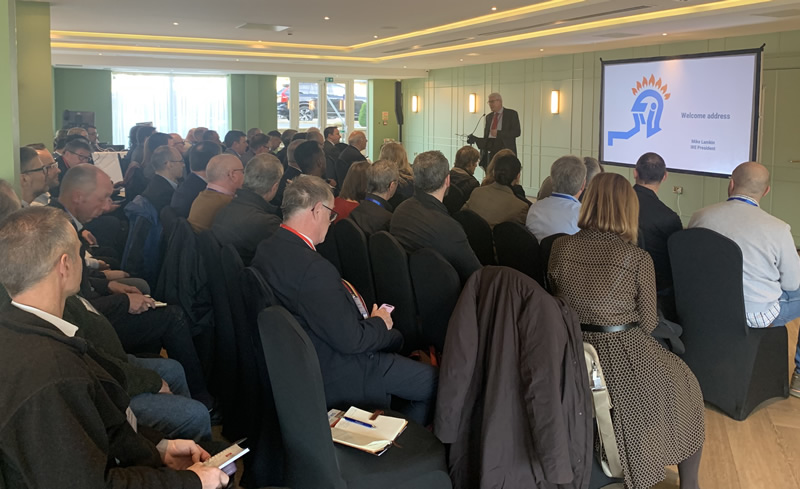
A full day’s technical programme considered some of the most important questions around how refractories will fit into a greener world and the technologies and expertise being developed to ensure lower carbon manufacturing. One of the main themes was to expel some of the so-called “myths” and fear surrounding hydrogen, which has in fact, said Tony Kinsella of Lucideon, been used in industry “for many years”. He looked at the twelve colours of hydrogen. He explained that whilst hydrogen remains an option, it is not a replacement for natural gas, meaning there is much complex debate still to be had in the industry, especially around burners, which would need to differ from existing systems. Another current barrier to its use being availability in the levels that will be needed.
Dave Bell considered the whole supply chain and embedded CO2. He said: “We have looked at making refractory performance better, despite the use of pure materials and whatever the material cost. Now we need to think about the energy used in making those materials. We have spent our time looking at making it easier for the user and have thus used high temperature to achieve these products. We might need to think about changing direction.” He considered the trends that are taking the industry in the direction of almost zero CO2 refractory, such as recycled by-products, resin-bonded and Geopolymer.
Speaking about the importance of the sustainability of recycled refractories, Melvyn Bradley of Tech-Ref Services said not all the three p’s are often considered. “We concentrate on the ‘planet’ part, but we must also remember that ‘profit’ is also critical for long term development,” he said. He warned: “Three quarters of refractory raw material is still coming from China, resulting in logistical challenges, availability squeeze, shipping route issues, inconsistent quality and geopolitics.”
In his presentation entitled: ‘Hydrogen resistance of refractories based on synthetic alumina raw materials,’ Sebastian Klaus of Almatis said there were “significant challenges” to meet the EU Green Deal. He claimed: “Steel must be a part of the solution – using hydrogen as a reducing agent. Hydrogen as a process gas has been used in the petrochemical industry for many years. He highlighted some experimental results from a joint research project investigating castables.
Chris Parr of Imerys spoke of the cost implications of a low carbon world in his presentation, ‘Alumina containing insulating materials for refractory products and their contribution to a low carbon world.’ He told delegates: “Firstly, you go for the easier targets to reduce CO2. Energy efficiency and recovery is almost free, but moving towards fuel switching/biomass etc. is more costly.” When looking at the barriers to insulating products he noted the difference between performance of bricks versus monolithics. “Air management becomes key,” he said, “to combat the ‘Swiss cheese’ problem”.
Adam Bell of Liberty Steel highlighted some of the techniques used by the company to return to ladle scanning and the value that has made in terms of measurement and performance. The performance of refractories was also an important aspect of the presentation by Steven Reumschussel of Saveway, entitled ‘Sustainable use of refractory materials by increase of lining life of coreless induction furnaces.’ “Waste can be a resource,” Robert Coggin of Capital Refractories enthused in his presentation ‘Reduced downtime and energy saving in incinerator plants.’ He said: “Energy from waste is part of the EU Waste Framework. There are 52 energy from waste incinerators, plus 66 under construction. However, they are controversial as the CO2 footprint is similar to coal.”
Chris Windle of DSF Refractories presented a paper entitled ‘Too damn hot, or is it?’ which considered the manufacture of carbon black. He said: “We are talking today about removing carbon, but we need it. It’s an essential ingredient of modern existence. Carbon black gives you durability.” He then looked at the five tenets for successful refractory lining.
The event concluded with dinner and entertainment in the evening. A training day entitled: ‘Beyond the Data Sheet’ was held on the following day (14 November 2025). The IRE thanks all the sponsors, presenters and attendees for their continued support. A full report on the event will be published in the March 2025 issue of The Refractories Engineer.
#IRE #Institute #Refractories #Engineers #Journal #Conference #Training